[authors: Tom Sumner and Tim Masten]
1st Edition
Overview
When you perform a site visit, you have two goals: collect the information needed to make a proper determination and get home safely to your family. While some hazards are readily visible and easily noticeable, others are hidden. Whether it’s a roof evaluation or a major fire to a manufacturing plant, being properly prepared for site hazards with adequate equipment for access and personal protective equipment (PPE) is paramount. But how do you know what to plan for to ensure a safe site visit?
You may have heard it referred to as Job Hazard Analysis (JHA), Activity Hazard Analysis (AHA), Workplace Hazard Assessment (WHA), Job Safety Analysis (JSA) or some other name. Regardless of the terminology used, all boil down to the same thing – integrating accepted safety and health principles and practices into a particular task or job operation. In this paper, we will be referring to this procedure as a JSA. The purpose of the JSA is to identify potential hazards and to mitigate their exposure through control methods that establish the safest way to perform each task of the job. A JSA focuses on the relationship between the worker, the task, the tools, and the work environment.
Benefits of a Safe & Healthy Workplace
A safe and healthy workplace not only protects workers from injury and illness, it can also lower injury/illness costs, reduce absenteeism and turnover, increase productivity and quality, and raise employee morale. For insurance professionals, an assignment may often involve conducting an inspection of a property that has experienced building damage, which poses hazards and potential hazards that are ever changing and unique to each project site.
By routinely conducting a JSA prior to work on each project, safety is enhanced while also complying with federal worker protection standards. OSHA’s Code of Federal Regulations (CFR) Standard 1910.132(d)(1)&(2) states:
“The employer shall assess the workplace to determine if hazards are present, or are likely to be present, which necessitate the use of personal protective equipment (PPE).“
… and …
“The employer shall verify that the required workplace hazard assessment has been performed through a written certification that identifies the workplace evaluated; the person certifying that the evaluation has been performed; the date(s) of the hazard assessment; and, which identifies the document as a certification of hazard assessment.”
OSHA requires a written certification that the hazard assessment has been performed. While there is no requirement that the hazard assessment itself be in writing, most professionals recommend that written documentation of the actual assessment should be a best practice.
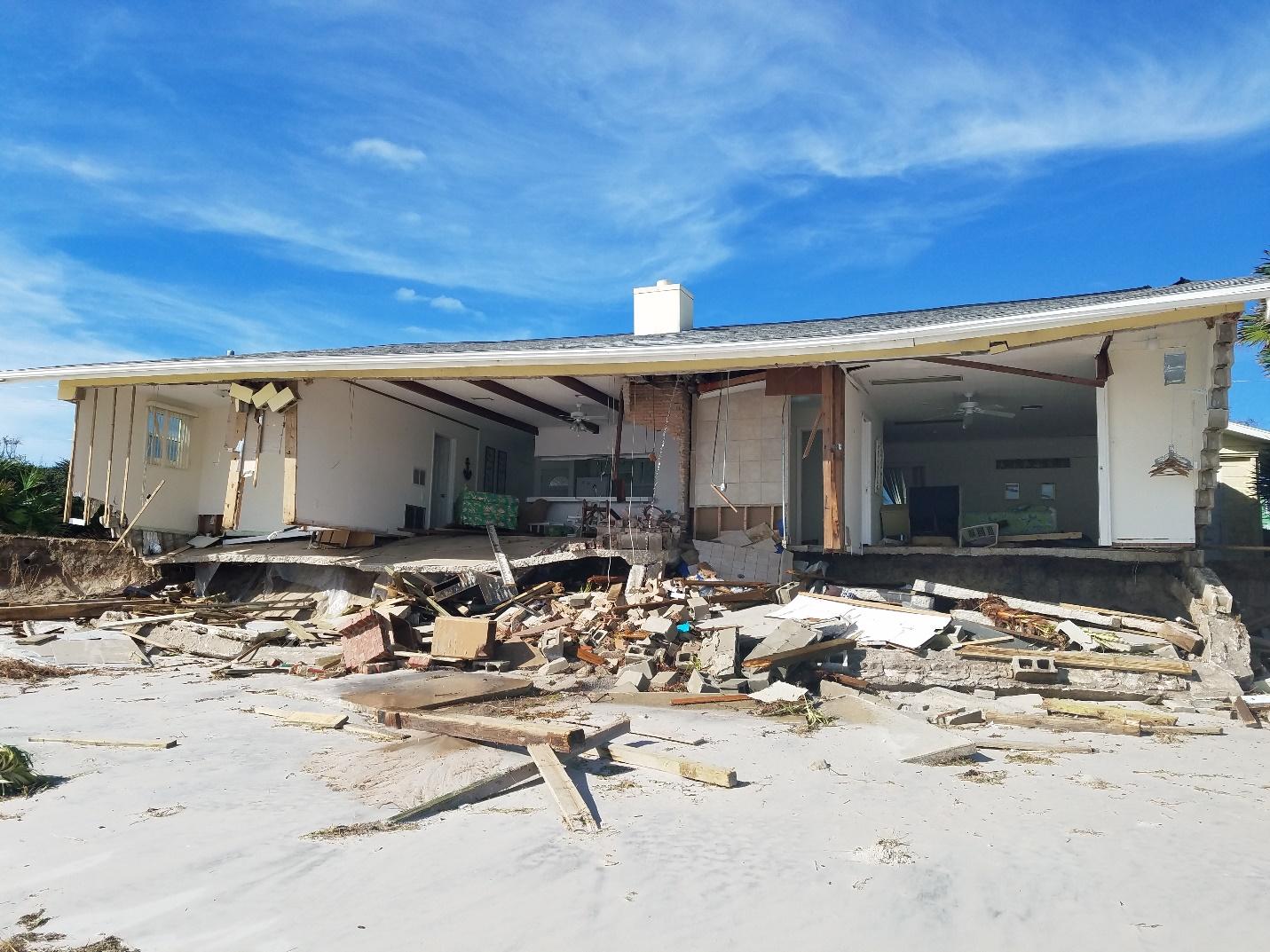
Figure 1 – Loss Site After a Hurricane
Creating a Job Safety Analysis
Effective risk management starts with identifying and addressing hazards before incidents occur. The challenges of carrying out a JSA often derail companies from completing them. Without a solid understanding of the hazards and risks your employees face with the tasks they accomplish each day, it’s difficult to remain consistent with safety.
Here are the steps to perform a thorough analysis of a job site:
-
Identify and document all job tasks or categories of job tasks that will be included in the process. Be thorough and detailed; list each step in the process sequentially.
-
Identify and document the hazards associated with each task or category of tasks. Consider all types of potential hazards: physical, chemical, and environmental.
-
Using the hierarchy of controls as shown in the diagram below. Identify and document the controls that must be used to control any identified hazards. It may be necessary to list multiple controls for a single step in the process.
-
Identify and document any required training or general PPE required for the identified tasks and any other general control measures needed.
-
List all contributors to the JSA. The JSA process shall be a collaborative effort between the supervisor or principal investigator and the personnel that will performing the identified task(s).
How to Identify Potential Hazards
Once these preliminary steps have been recorded, potential hazards must be identified. Based on observations of the job, knowledge of accident and injury causes, and personal experience, list the things that could go wrong at each step. To help identify potential hazards consider questions such as:
-
Can any body part get caught in or between objects?
-
Do tools, machines, or equipment present any hazards?
-
Can the worker make harmful contact with moving objects?
-
Can the worker slip, trip, or fall?
-
Can the worker suffer strain from lifting, pushing, or pulling?
-
Is the worker exposed to extreme heat or cold?
-
Is excessive noise or vibration a problem?
-
Is there a danger from falling objects?
-
Is lighting a problem?
-
Can weather conditions affect safety?
-
Is harmful radiation a possibility? (including sun exposure)
-
Can contact be made with hot, toxic, or caustic products?
-
Are there dusts, fumes, mists, or vapors in the air?
-
Is there a potential for asbestos to be disturbed?
-
Are there other contractors on site performing unsafe acts?
A job hazard analysis is an exercise in detective work. Your goal is to discover the following:
What can go wrong? For example, by determining how old the property is, you may need to be concerned about asbestos, lead based paint, or mold.
What are the consequences? A fall from a ladder could have immediate consequences. By using the proper ladder, inspecting it for defects, staging it on a level, solid surface, and applying the ‘three points of contact’ rule, you can better mitigate the consequences of a fall. Prolonged exposure to asbestos, lead-based paint, or mold could have long-term consequences. Following proper protocols during renovation or repair, when disturbing potential or known materials containing these hazards, reduces the risk of health impacts down the road.
How could it arise? Unforeseen problems can arise at any time; even a task as simple as an attic inspection cannot be overlooked. Floors can collapse and attics can be tight, dangerously hot spaces. Nails hidden in insulation and bats carrying diseases could also present health and safety issues.
What are other contributing factors? Accidents are rarely the result of one action and are more often the result of several sequential breakdowns in procedural systems. Stay aware of all things including tidiness and organization of job sites, which could indicate weakness in discipline and all things safety.
How likely is it that the hazard will occur? Experience is crucial to fully evaluate this question. Reach out to another expert for help if you come across something new that poses a potential threat to health and safety.
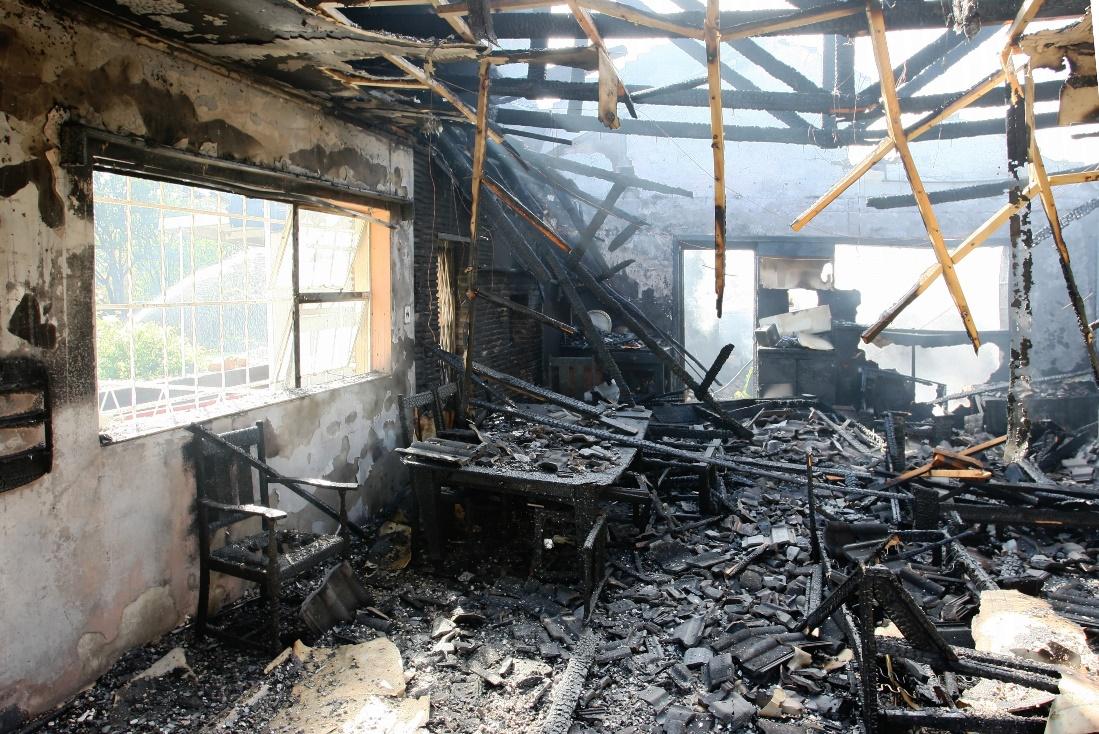
Figure 2 – Loss Site After a Structural Fire
To make your job hazard analysis useful, document the answers to these questions in a consistent manner. Describing a hazard in this way helps to ensure that your efforts to eliminate the hazard and implement hazard controls help target the most important contributors to the issue at hand. Good hazard scenarios describe:
• Where it is happening (Environment),
• Who or what it is happening to (Exposure),
• What precipitates the hazard (Trigger),
• The outcome that would occur should it happen (Consequence), and;
• Any other contributing factors.
How to Minimize or Prevent the Hazard(s)
The hierarchy of control creates a systematic approach to managing safety in your workplace by providing a structure to select the most effective control measures that eliminate or reduce the risk of certain hazards stemming from business operations.
The hierarchy of control has six levels of control measures, the most effective measure is at the top of the hierarchy and the least effective is at the bottom. You always start from the top of the hierarchy chart then work your way down.
The hierarchy of control involves these important steps:
-
Elimination – removes the cause of danger completely (e.g., performance of a hazardous job in a non-hazardous way). This may include using a fixed ladder system that is in good condition to access a roof as opposed to using an extension ladder.
-
Substitution – controls the hazard by replacing it with a less risky way to achieve the same outcome (e.g., replacing a harsh solvent chemical for cleaning equipment with a non-hazardous cleaner/degreaser).
-
Isolation – separates the hazard from the people at risk by isolating it (e.g., lock-out/tag-out procedures that deenergize a piece of equipment).
-
Engineering – using engineering controls (i.e., making physical changes, to lessen any remaining risk – e.g., redesign a machine by adding safeguards or introducing machinery that removes the hazard – e.g., use of exhaust fans to extract atmospheric hazards).
-
Administration – use administrative controls to lessen the risk (e.g., install signs or rotate jobs).
-
Personal Protective Equipment (PPE) – require your employees to wear PPE (e.g., provide gloves, earplugs, goggles, respirators, iridescent vests, steel toe shoes and ensure employees are trained in the use, care, and maintenance of all PPE while always inspecting before use).
Note: The use of PPE to control hazards should always be the last resort. Do not select a control based on ease of implementation.
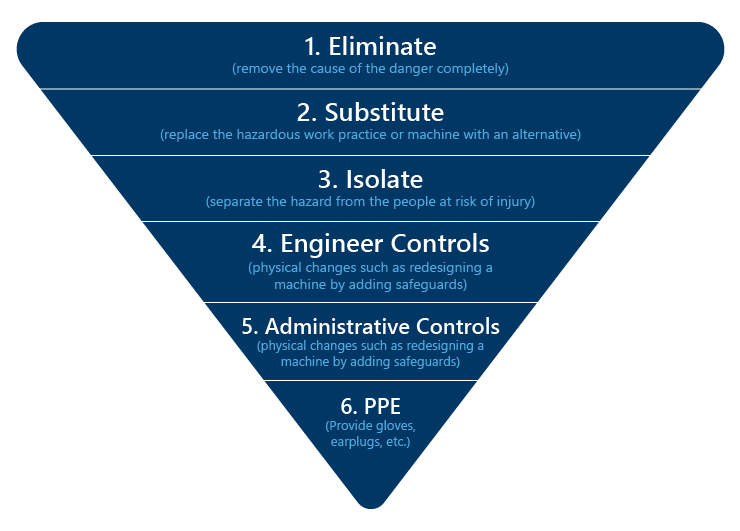
Figure 3 – Hierarchy of Control
The circumstances and environment of project sites are often in a state of constant change. In a short period of time, several rooms or even whole floors of damaged material may be been torn out. When any aspect of a job site changes with respect to new materials, new equipment, new methods, or new environments that could cause a hazard, which would require a JSA to be performed again.
If a serious accident occurs on site, a new JSA may help to identify the cause of the accident and determine methods to prevent any future incidents.
Conclusion
Remember, not all hazards are immediately apparent and could be undetectable through site and smell alone. Safety analyses are not a sometime thing, they are an integral step in the assessment process and must be properly executed. Asking the right questions, considering possible outcomes, and following necessary safety protocols during every site inspection ensures compliance and reduces risk, allowing for the site to be evaluated in an effective manner.
References