* All information and comments are as of 14 April 2025.
Recent tariff-related developments and implications for trade and logistics
The global trade landscape is shifting, with tariffs largely being used as strategic instruments in economic and geopolitical competition.
In early April 2025, the United States introduced a sweeping new tariff regime, including a general 10% import tariff on nearly all goods entering the country. The government announced country-specific tariff rates ranging from 11% to 50% on imports from dozens of trading partners and imposed tariffs of 125% on Chinese goods.
While this across-the-board tariff of 10% remains in force, the implementation of additional reciprocal tariffs – targeting selected countries with a trade surplus with the US – has been temporarily suspended for 90 days to allow for bilateral negotiations. These reciprocal tariffs remain under consideration.
The 90-day suspension does not apply to Chinese goods. Tariffs on Chinese imports have been increased to 145% with immediate effect (comprising an existing 20% tariff introduced in February 2025 and an additional 125% punitive tariff implemented on 9 April 2025). Certain electronics, including smartphones and computers, have been temporarily exempted from the increased tariffs, remaining subject to the existing 20% rate.
Although framed as a major shift in trade policy, the measures build on earlier tariff actions affecting specific countries and sectors, including China, steel, aluminium and automobiles. Some of these earlier tariffs have been imposed, suspended and re-imposed over time. The current package will likely be applied cumulatively in practice.
While the full scope and timing of the final regime are still evolving, the tariffs carry significant legal and commercial implications – particularly for businesses engaged in cross-border trade, transport and logistics. Many are now facing unclear or shifting tariff liabilities, complex country-specific rules and increased pressure to monitor bilateral developments closely.
Several major US trading partners have announced or implemented counter-measures, while other countries are either following suit or indicating that similar actions may be taken in response to US tariffs. Risks of a “tariff cascade”, through which other countries enact safeguards against the anticipated diversion of products from the US to other export markets, are also rising.
China and the European Union were among the first to respond to the US tariff announcement, but their reactions have differed significantly. China has imposed retaliatory additional tariffs on selected US goods, to which the United States has already responded, with tariff levels on Chinese goods now substantially higher. In contrast, most other major trading partners – including the EU, the UK, Japan and Canada – have not introduced retaliatory measures at this stage. Instead, they have entered into discussions with the United States following the announcement of the 90-day pause on the implementation of “reciprocal tariffs” referred to above.
These developments reflect a broader trend: the use of tariffs and other trade regulations more widely as tools to pursue industrial, strategic or political objectives.
In line with this shift in approach, the US is preparing to impose additional port fees on Chinese-built vessels and Chinese-operated vessels in an effort to counter Chinese dominance of the maritime sector.
Much now depends on the outcome of bilateral negotiations, particularly between the US and China, where tensions remain elevated.
As a result of these developments and the potential for future changes, businesses engaged in international trade – including exporters, importers, transport operators and logistics providers – now operate in a fast-changing and uncertain environment. Tariffs may change with little or no warning, affecting delivery routes, sourcing strategies, pricing structures, contractual obligations and many other matters relevant to international trade, transport and logistics.
In this new landscape, the ability to monitor, interpret and adapt to evolving tariff regimes may be critical. Companies are encouraged to closely collaborate with transport and logistics providers and customers to maintain resilient supply and delivery chains, avoid unnecessary costs and ensure continued access to key markets.
Companies may respond by developing and applying new operational practices and strategic approaches tailored to evolving trade conditions. Transport and logistics providers can design and offer new or adapted services and delivery models that address emerging challenges, while their customers can integrate these solutions into their own supply and distribution systems. Through such coordinated efforts, both providers and customers may enhance resilience, improve efficiency and secure competitive or strategic advantages in an increasingly complex and uncertain environment.
Overview of key developments – useful links
Given the pace and complexity of recent trade developments and the likelihood of further rapid changes, we encourage companies to continuously monitor specific tariff measures and responses.
A regularly updated summary of US trade actions and related global responses is available on the DLA Piper website:
Tracking Trump Tariffs – DLA Piper insight hub
This page includes current overviews of the general 10% US import tariff, sector-specific measures and international reactions by major trading partners. It also provides links to recent articles, legal updates and insights into the US tariffs’ implications for global supply chains and cross-border business operations.
For information regarding the EU’s, the UK’s and Asian countries’ intended responses to the tariffs, please refer to the following article:
Trump Administration tariffs: Responses from the EU, the UK, and APAC
Note that, among the contemplated measures, the EU is exploring the deployment of the Anti-Coercion Instrument (Regulation 2023/2675) (ACI). This is a legal instrument that empowers the EU to respond to economic coercion by third countries through a variety of measures - some of which may have broad implications for the transport and logistics sector. For instance, the ACI may lead the EU to the imposition or re-imposition of customs duties (including duties beyond most-favoured nation level), import/export controls (including through quotas and licences) and restrictions on the transit of goods.
The ACI is not merely a theoretical tool – it has entered into force and may be activated swiftly in response to recent US tariff measures. Several EU officials have signalled their readiness to deploy it in practice should negotiations fail to reduce tensions and possibly conflicting measures and actions.
Affected products, flows and logistics markets
The rapidly expanding tariff landscape bears significant implications for the global movement of goods and the logistics systems that support it.
The goods most directly affected include machinery, electronics, vehicles, industrial components, chemicals, metals and a wide range of agricultural and consumer products. These sectors often rely on complex, multi-country supply and delivery chains – making them particularly vulnerable to new trade barriers and cost increases.
Transport flows are being disrupted as companies react to shifting tariffs and retaliatory measures. Imports of Chinese machinery and industrial electronics into the United States have slowed sharply in the face of combined duties exceeding 100%, although certain categories – including certain consumer electronics such as mobile phones, laptops, tablets, monitors and other consumer IT devices – have recently been temporarily exempted. Exports of US agricultural products to China have also declined due to retaliatory tariffs.
At the same time, some European and US manufacturers are exploring ways to bypass tariff exposure by adjusting production and shipping strategies – for example, by shifting assembly operations to neutral countries or rerouting goods through low-tariff regions. For example, several electronics manufacturers have shifted final assembly from China to Vietnam, using ports in Thailand or Malaysia to access the US market. In Europe, automotive components are increasingly routed via Turkey to avoid direct exposure to US and Chinese duties.
This realignment is already visible in global logistics markets. Container shipping between China and the US is experiencing reduced volumes, while routes connecting Southeast Asia, the Middle East and Latin America are becoming more attractive for both sourcing and transit. Air freight providers are seeing increased demand for time-sensitive shipments of components where alternative routes have become longer or more complex. Freight forwarders and customs brokers are under pressure to recalculate delivery models and landed costs on short notice, while multimodal operators are exploring new combinations of road, rail, sea and air to maintain flow continuity.
For transport and logistics providers, these developments could mean increased uncertainty in planning and execution, greater volatility in volumes and revenue and a growing need to offer value-added services such as customs advisory, tariff monitoring and flexible warehousing. For customers, the stakes are equally high: choosing the wrong routing or International Commercial Term (Incoterm) could result in significant financial losses or delivery failure.
Examples of affected goods and logistics implications
- Machinery and industrial components
– high tariffs on Chinese, Indian and European goods entering the US
– increased need for origin documentation and product classification
- Automotive and transport equipment
– tariffs on EU-, Asia-, Mexico- and Canada-manufactured cars and parts (announced or anticipated)
– shift towards regional assembly and alternative sourcing routes to reduce tariff exposure
– Mexico and Canada play a key role in many automotive supply chains – including for EU and Asian manufacturers – raising additional exposure concerns
- Consumer electronics
– certain consumer electronics, such as mobile phones, laptops, tablets and monitors, have recently been temporarily exempted from US tariffs on imports from China
– US tariffs still apply to imports of some consumer electronics from Southeast Asia
– increased use of bonded warehouses and just-in-case logistics amid ongoing policy uncertainty
- Food and agricultural products
– chinese retaliation on key US exports like soy, pork and citrus
– pressure on cold chain logistics and rerouting of time-sensitive cargo
- Chemicals and metals
– bilateral tariffs between US and Asia affecting steel, aluminium and fertilisers
– port congestion and longer customs clearance procedures in high-risk lanes
Disruption risks in supply and delivery chains
The current wave of tariff actions has introduced major disruption risks across both supply chains and delivery chains.
For companies that depend on international movement of goods – whether as producers, exporters, importers or service providers – the risk of interruption, delay or cost escalation has increased sharply.
The tariffs have led some businesses to suspend purchases, delay contracts or urgently seek alternative suppliers – often with limited notice or reduced quality control. In sectors reliant on specialised components or raw materials, such disruptions may affect entire production runs or customer deliveries.
On the delivery side, higher tariffs and retaliatory measures have prompted order cancellations, renegotiations of contract terms and changes in destination markets. In many instances, goods already in transit are now subject to new duties or clearance procedures, creating unexpected bottlenecks and the need to re-route or warehouse stock temporarily.
Many companies are also experiencing indirect disruptions – for example, where a sub-supplier is affected by tariffs and cannot fulfil its obligations, which then delays downstream processes. Logistics providers report that just-in-time delivery models are becoming increasingly difficult to maintain, particularly on long-haul routes with increased customs complexity or in sectors with tight quality and safety requirements.
Even where transport itself is not directly disrupted, uncertainty about actual or potential tariffs and administrative burdens could delay decision-making and lead to conservative stock strategies, with ripple effects throughout the chain. This uncertainty also complicates planning for transport capacity, especially in volatile corridors such as trans-Pacific and transatlantic lanes.
Key disruption risks affecting supply and delivery chains
- sudden cost increases due to new or updated tariffs on goods in transit
- delays linked to new customs documentation and inspection procedures
- contract renegotiations or cancellations due to tariff-driven price shifts
- dependency on single-source suppliers in tariff-affected countries
- breakdown of just-in-time flows, resulting in increased inventory holding
- rerouting needs triggering last-minute adjustments in transport planning
- limited visibility across complex supplier tiers, especially in global chains
Contracts, risk allocation and dispute resolution in a changing tariff landscape
Contractual risks arising from tariffs and regulatory change
Recent tariff measures have created considerable uncertainty for businesses engaged in international trade, transport and logistics. Contractual frameworks that were developed under relatively stable conditions may no longer adequately allocate risks, obligations and rights under new and changing conditions and regulatory schemes. Sudden increases in customs duties, reclassification of goods, new licensing or inspection requirements and administrative delays at borders can affect activities, processes, costs, timing and even legal compliance.
This has significant implications for sellers and buyers of goods, as well as for logistics and transport service providers. For example, if a shipment is delayed or stopped at the border due to a new classification or licensing requirement, who bears the additional storage costs or penalties? If tariffs are increased after goods are dispatched but before delivery, which party absorbs the cost difference? And if goods are rerouted or returned due to non-compliance, who bears the cost and legal responsibility?
For logistics and transport providers, such situations may require rerouting, rebooking, repackaging or urgent re-documentation, all of which carry time and cost burdens. These service providers may be exposed to claims if customers perceive a failure in execution, even where causes are regulatory. At the same time, proactive and well-structured service offerings – such as customs monitoring, tariff advisory and route optimisation – could create added value and competitive advantage.
The financial and operational consequences of these scenarios can be serious, particularly in sectors operating on fixed-price contracts or low margins. With this, companies are encouraged to explicitly address such risks and costs in their contracts, and to continuously assess their exposure – especially in sectors with integrated supply and delivery chains.
Incoterms and their contractual effects and impacts
Incoterms published by the International Chamber of Commerce (ICC) are widely used to define the responsibilities of sellers and buyers in cross-border transactions. They govern matters such as delivery, transfer of risk, allocation of transport and customs costs, and documentation.
The following are two commonly used Incoterms:
- Delivered Duty Paid (DDP): The seller is responsible for delivering the goods to the buyer's destination and bears all costs, including transport, export and import duties, customs clearance, and insurance.
- Implication: Under DDP, sellers carry the full burden of new tariffs or procedural delays. This may severely impact margins if new duties are introduced suddenly. For transport and logistics providers, DDP contracts may require greater involvement in customs clearance and final-mile coordination, which may increase service complexity, costs and liability.
- Free On Board (FOB): The seller delivers the goods to a designated port and loads them onto the buyer's ship. Risk and responsibility transfer to the buyer once the goods are on board.
- Implication: Under FOB, buyers assume risk earlier in the transport chain and may be more directly exposed to destination-country tariffs or clearance issues. Logistics providers acting for the buyer are encouraged to ensure correct documentation and coordination at the port of loading, as mistakes could create costs and liability.
Other Incoterms, such as Cost, Insurance and Freight (CIF) or Ex Works (EXW), allocate responsibilities differently and may offer varying levels of exposure and control. For example, under EXW, the buyer assumes responsibility from the seller's premises, which can be risky if the buyer is unfamiliar with export procedures or local customs rules.
The choice of Incoterm affects not only legal obligations but also operational execution and costs and insurance arrangements. It is important for all parties – including transport and logistics providers – to understand these terms and their practical impact. The right choice of Incoterm may improve efficiency, reduce costs, minimise dispute risk and clarify who does what in the event of changes tariffs or others related changes or disruptions.
Transport and logistics agreements: allocating responsibilities and costs
Transport and logistics providers operate under increasingly complex global conditions. Under traditional models, many logistics agreements are based on assumed stability in customs regimes and transport routes. However, in the current environment, companies are encouraged to define and regulate roles and responsibilities in detail.
Matters to address include (among many other matters):
- Who is responsible for monitoring and reacting to tariff and regulatory changes?
- Who provides and verifies documentation (for example, certificates of origin, classification codes and shipping and transport documents)?
- How are costs for customs brokerage, warehousing, demurrage, inspections, storage or re-routing handled?
- Are rate structures flexible enough to accommodate sudden regulatory costs and procedural delays?
For transport and logistics providers, unclear allocation of such responsibilities could lead to claims for delay, non-performance or cost overruns. In turn, this could trigger conflicts with subcontractors or upstream providers. For buyers and sellers, gaps in logistics contracts can translate into financial risk or costs, loss of goods or reputational damage. In their contracts, providers are encouraged to set clear expectations for what is included in the service scope, how costs are calculated and allocated, and how requirements and exceptions are managed and met.
Well-drafted agreements can also create opportunities: service providers offering flexible, transparent and customs-adapted solutions may strengthen their client relationships and services and differentiate themselves in the market.
Force majeure, hardship and change of law clauses
Many contracts include clauses intended to deal with extraordinary events:
- Force majeure typically covers unforeseeable events outside a party’s control, which prevent contractual performance. Force majeure may for example include war, natural disasters, strikes and changes in laws, regulations or tariffs or other customs duties.
- Hardship may apply when performance becomes excessively burdensome due to changed circumstances. This may for example include steep tariff increases or major currency fluctuations.
- Change of law provisions address the legal consequences of new laws or regulations or government-imposed restrictions. This may for example include sudden export or import bans or licensing obligations).
However, these clauses vary in scope, effects and enforceability. Not all tariff changes will qualify as force majeure, especially if such changes are increasingly common. Hardship may not be triggered unless the impact is severe and clearly documented. Change of law clauses can offer more predictable protection but generally must be carefully drafted to cover relevant jurisdictions and types of legal change.
Transport and logistics providers, as well as their customers, are encouraged to review these clauses with regard to cross-border obligations. Clauses should consider practical realities: Will delivery routes need to change? Will customs delays create breach risks? Will force majeure protect only against non-performance or also allow temporary suspension?
Dispute resolution: mechanisms and risk mitigation
Contractual uncertainty could increase the likelihood of disputes, especially when costs rise unexpectedly, responsibilities are unclear or deliveries are delayed. Disagreements may concern matters such as the following:
- Who pays for new or increased tariffs?
- Who is responsible for providing updated documentation or responding to customs requests?
- Is a party entitled to terminate or suspend performance?
- Are there grounds for compensation, indemnity or renegotiation?
To manage such and other risks, contracts should generally include clear and effective dispute resolution procedures. These might involve:
- stepped resolution clauses: requiring negotiation, internal escalation or mediation before formal legal proceedings
- arbitration agreements: offering faster, confidential resolution, often preferred in international logistics
- jurisdiction and applicable law clauses: identifying the rules that govern any dispute, especially important where multiple countries are involved
Dispute clauses should generally be practical, not just formal. In time-critical supply chains, rapid interim measures may be more valuable than lengthy litigation. In their contracts, companies are also encouraged to address record-keeping obligations to support claims and responses.
Close communication between logistics providers and their clients during evolving situations may prevent misunderstandings from escalating into legal conflicts.
Examples of contractual risks and mitigation measures Checklist: documentation essentials under heightened tariff regimes
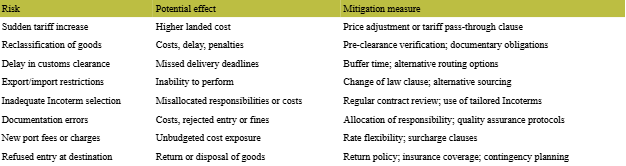
Checklist: documentation essentials under heightened tariff regimes
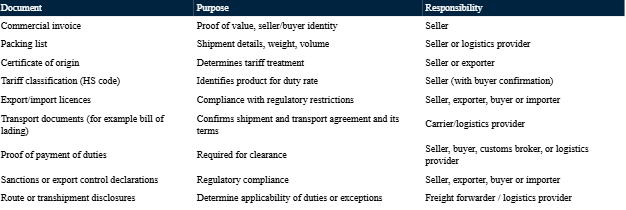
Clear allocation and timely preparation of these documents may help avoid and reduce risks, costs, delays, penalties and disputes.
Transport and logistics providers often play a central role in coordinating and validating this documentation. Contracts should reflect their obligations clearly.
By carefully reviewing contractual terms, updating documentation processes and maintaining close coordination between sellers, buyers and logistics providers, businesses may better manage the complex risks presented by the evolving tariff landscape. Clear definitions, flexible pricing models and well-drafted dispute clauses are often important components of resilient cross-border operations.
While contracts define roles and responsibilities, successful execution can also depend on accurate and timely compliance with customs procedures. This is addressed in the next section.
Customs procedures and documentation obligations
Beyond contractual frameworks, the practical implementation of customs rules and documentation requirements is often equally critical. This section outlines the operational obligations and challenges businesses must navigate in day-to-day cross-border trade and logistics under the current and evolving tariff landscape.
The expansion of tariffs across multiple trade lanes has significantly increased the importance and complexity of customs procedures.
For both transport and logistics providers and their customers, accurate documentation and compliance with new rules are now essential to avoid delays, fines or rejection of goods at the border.
Each new or increased tariff measure brings with it updated requirements for product classification, proof of origin and transaction documentation. In some jurisdictions, special permits or product-specific declarations must be submitted in advance. Even minor discrepancies in customs paperwork can now result in extended inspections or full revaluation of duties, which can, in turn, disrupt planned delivery schedules.
Transport and logistics providers play a central role in this environment, especially freight forwarders, customs brokers and third-party logistics companies that handle border formalities. These providers are encouraged to align their processes with the latest regulatory requirements in both exporting and importing countries, and communicate proactively with customers about any issues or risks.
Equally, exporters and importers must ensure that product data is accurate and provided in good time. This includes tariff classification under the Harmonised System (HS), transaction value documentation, and all required certificates of origin – particularly where preferential trade agreements are still applicable despite general tariff increases.
The rise in tariff-related compliance obligations has also highlighted the value of simplified customs procedures. Companies operating under Authorised Economic Operator (AEO) status or approved trusted trader schemes report fewer delays and better predictability. However, participation in such schemes requires documented internal procedures and ongoing audit-readiness.
Checklist: documentation steps under heightened tariff regimes
- ensure accurate HS classification of all goods being traded
- obtain and verify valid certificates of origin where required
- align invoices, packing lists and shipping documents in all details
- document transaction value and include Incoterms references
- submit any product-specific declarations or permits in advance
- maintain records of supplier declarations and manufacturing origin
- monitor for updates in customs rules and clearance thresholds
- coordinate internally across logistics, sales and legal teams
- consider applying for Authorised Economic Operator (AEO) authorisation or similar simplified customs status
Strategic responses and commercial adjustments
In today's rapidly evolving trade environment, businesses in both the transport and logistics sector and the broader supply chain are encouraged to consider structural and strategic adjustments to reduce tariff exposure and maintain continuity in cross-border trade.
These adjustments may involve rethinking sourcing decisions, modifying delivery flows and redesigning operational setups to remain competitive and compliant.
One immediate strategy could be to diversify suppliers and production locations to avoid excessive dependence on countries subject to high or unstable tariffs. For example, several European and North American manufacturers are relocating certain operations from China to Southeast Asia or Eastern Europe.
Another possible measure is the use of regional distribution centres, bonded warehouses and free trade zones. These facilities offer greater flexibility in routing, customs clearance timing and inventory planning. By deferring final customs processing until closer to the end-customer, businesses can often respond more dynamically to tariff changes and reroute goods as needed.
From a transport logistics perspective, many providers are expanding their use of multimodal and adaptive routing. Combining road, rail, sea and air transport could enable faster response to disruption and help avoid congested or high-risk ports. Some providers are also investing in digital solutions that automate tariff classification, monitor trade policy changes and optimise routing decisions in near-real time.
At the same time, transport and logistics providers are facing growing pressure on capacity and pricing. Some shipping lines have reduced space allocations on affected trade lanes, and price adjustments are increasingly being seen at terminals and inland hubs due to longer dwell times, compliance requirements or changes in demand patterns. These developments are pushing many logistics operators to reallocate resources and adjust commercial terms – with implications for both their own planning and their customers' cost structures.
While much of the focus is on the strategic responses of transport customers and users – such as manufacturers, importers and retailers – the challenges and adaptations required by transport and logistics service providers are distinct but closely linked. For example, customers and users may need new routing models or Incoterm allocations, while service providers may need to rebalance network design or renegotiate service levels. Recognising this distinction may be essential in ensuring both sides of the supply relationship respond appropriately to trade volatility.
In parallel, some businesses are reorganising their internal structures – for instance, by establishing subsidiaries in key markets to enable domestic sale and distribution, thereby reducing the need to import finished goods across tariff barriers. Others are renegotiating pricing models with suppliers and customers to reflect shared exposure to duties and clearance costs.
Potential strategic and commercial adjustments for transport and logistics customers and users
- diversify sourcing to include countries outside high-tariff zones
- use bonded warehouses or free zones to delay customs clearance
- establish regional hubs for assembly, packaging or final processing
- shift from global to regional delivery models where feasible
- restructure internal supply chains to reduce cross-border flows
- renegotiate pricing and Incoterms with suppliers and customers
- invest in compliance capabilities, such as customs knowledge and documentation workflows
- monitor trade policy changes and use trade intelligence to support planning
Possible strategic and operational responses for transport and logistics service providers
- rebalance network capacity and routing across affected trade lanes
- offer flexible warehousing, including bonded storage options
- adapt terminal handling and storage pricing to reflect delays and capacity shifts
- expand multimodal services to maintain continuity in disrupted lanes
- adjust schedules and capacity allocations in response to trade volatility
- update standard service agreements to reflect tariff and customs-related risks
- train staff in new customs regimes and integrate digital compliance tools
- provide monitoring and advisory services on tariffs and trade policy changes
Considerations transport and logistics providers and trade-dependent businesses
In a trade environment increasingly shaped by tariffs, regulatory change and geopolitical tension, both transport and logistics service providers and their customers are encouraged to take proactive steps to strengthen their resilience and adaptability.
Whether acting as carriers, freight forwarders, importers, exporters or intermediaries, transport and logistics companies are encouraged to develop a structured approach to managing customs-related risks and responding to new trade barriers.
Transport and logistics providers often play a critical role in helping clients navigate uncertainty. To do so effectively, they are encouraged to ensure that internal systems and contractual frameworks are aligned with the new realities of cross-border trade. This includes updating standard service agreements, refining customs clearance procedures and providing transparent communication around costs, routing changes and potential delays.
Customers – particularly manufacturers, distributors and retailers involved in international sourcing or export – are encouraged to integrate customs awareness into business planning, contract management and supply chain design. Working closely with transport and logistics partners and customs experts could prevent costly missteps and support faster recovery when trade conditions shift.
Importantly, both sides may benefit from building strong, information-rich partnerships that enable early identification of tariff-related risks and rapid adjustment to new circumstances.
Possible practical steps for transport and logistics providers
- Update client terms and service descriptions to reflect potential regulatory changes
- Provide tariff monitoring and advisory services as part of core offerings
- Train operations and customer-facing staff in updated customs requirements
- Strengthen digital systems for document handling and compliance tracking
- Engage with industry networks and authorities to stay informed about changes
- Develop contingency plans for rerouting and alternative capacity in key corridors
Possible practical steps for exporters, importers and supply chain operators
- Map tariff exposure across all sourcing and delivery routes
- Review and adjust Incoterms and risk allocation in contracts
- Strengthen internal customs handling processes and documentation workflows
- Build buffer stocks or regional warehousing to absorb delays and disruption
- Collaborate with logistics partners to develop flexible delivery strategies
- Monitor government announcements and use trade intelligence tools to stay ahead
Outlook – adapting transport and logistics to an uncertain trade environment
The growing use of tariffs by the US, the EU, China and other large economies is not an isolated trend – it could signal a broader transformation of the global trading system. Trade is increasingly shaped by unilateral actions, strategic competition and short-notice regulatory shifts.
This shift in global trade dynamics was recently acknowledged by UK Prime Minister Keir Starmer, who stated: “The world has changed, globalization is over and we are now in a new era.” His comment reflects a broader recognition among political leaders that previous assumptions about open markets and predictable trade flows may no longer hold. In this new environment, governments are increasingly turning to national interest-driven trade policy, and businesses must adapt to a less stable, more fragmented global system.
For transport and logistics, this could mean a permanent change in operating conditions. Access to global markets can no longer be taken for granted, and transport routes that were once stable may be rerouted or restructured in response to sudden policy changes. The same applies to customs requirements, import restrictions and documentation standards, which may vary sharply from one country or region to another.
This shift could require a new mindset. Tariffs and trade restrictions are no longer occasional irritants – they are now strategic variables that must be integrated into planning, pricing, contract management and risk mitigation. The ability to anticipate developments, interpret regulatory changes and act quickly across multiple markets has become a key competitive differentiator.
For transport and logistics providers, this could mean investing in systems, staff and services that support rapid adjustment and provide clients with clarity and confidence. For customers, it could mean strengthening internal processes, coordinating more closely with external partners, and re-evaluating the assumptions underlying sourcing and distribution strategies.
Ultimately, success in the emerging trade and tariffs landscape could depend not only on operational excellence, but on strategic awareness and collaborative execution. Those who can build and use flexible, well-informed, and resilient trade and transport models and solutions may be better positioned to navigate uncertainty – and to seize opportunities in new markets, partnerships and trade routes – as global patterns continue to evolve.
[View source.]