[author: Dr. Luaay Hussein]
Overview of Parking Garage Infrastructure and the Role of Structural Engineers
Reinforced concrete parking garages are a critical component of urban infrastructure, addressing the growing need for efficient parking solutions due to urbanization and increased vehicular demand. Parking garages play a vital role in ensuring the mobility and accessibility of individuals within urban areas, which is particularly crucial as cities expand and the number of vehicles on the roads rises. Efficiently designed and well-maintained parking structures contribute to the aesthetics and functionality of urban landscapes, optimizing land use and supporting sustainable development practices.
Generally, parking garages are susceptible to several deterioration mechanisms over time due to exposure to harsh conditions, usage, and inadequate maintenance. In cold climate regions such as Canada, parking garages are exposed to de-icing salts that accelerate the rate of steel corrosion and freeze and thaw cycles, compromising structural integrity.
The durability of parking garages largely depends on the quality of their design, construction, and ongoing maintenance. Structural engineers play a significant role in assessing their condition, ensuring their safety, and identifying potential issues before catastrophic failure.
This report explores the primary responsibilities, methodologies, key components, repair methods, and importance of structural engineers in the evaluation of parking garages.
Essential Structural Elements of Multi-Level Parking Garages
To understand the cause of deterioration in parking garages, it is essential to understand the components of multi-level parking garages. A typical multi-level parking garage consists of the following:
- Structural elements. Multi-level parking garages mainly consist of:
-
- Columns and beams. These are the primary structural components that support the weight of the structure and transfer the load to the foundation.
- Slabs. A concrete slab reinforced with steel bars forms the driving surface. It must withstand vehicular loads, environmental factors, and potential impact forces.
- Slab-on-grade. A concrete slab placed directly on the ground and generally reinforced with welded wire mesh.
- Ramps and staircases. Ramps and staircases facilitate vehicular and pedestrian movement between parking levels.
- Ventilation and lighting systems. Adequate ventilation and lighting systems are crucial for maintaining air quality, visibility, and user comfort in parking structures. Proper ventilation helps mitigate air pollutants, while adequate lighting enhances visibility and safety for users.
- A drainage system. An effective drainage system is installed to manage rainwater and prevent flooding in underground parking.
- A waterproofing system. Sealers and floor coatings are used as waterproofing systems in parking garages to prevent water infiltration.
- Expansion joints. Water-tight joints are used to control the thermal movement of the parking garage.
Parking Structure Concrete Deterioration
Concrete deterioration in parking structures may occur due to numerous factors, and addressing these issues is essential for maintaining the structural integrity and safety of the facility. Some of the common causes of concrete deterioration in parking garages include:
- Reinforcement corrosion. Steel reinforcement corrosion occurs due to the use of de-icing salts during the cold season to melt ice. Exposure to moisture and chloride ions in underground environments can accelerate the corrosion of embedded steel reinforcement in parking structures. Corrosion-induced expansion leads to cracking, spalling, and loss of structural integrity.
- Freeze-thaw cycling. In cold regions, freeze-thaw cycles cause water trapped in concrete pores to expand, resulting in cracking, surface deterioration, and structural weakening over time. Air-entrained concrete mixes and proper drainage systems help mitigate freeze-thaw damage.
- Abrasion and wear. Constant vehicular traffic and tire abrasion wear down concrete surfaces, leading to surface deterioration and loss of skid resistance. Durable concrete mixes, surface hardeners, and regular maintenance of traffic lanes help minimize abrasion and wear.
- Chemical attack. Exposure to aggressive chemicals such as oil, fuel, or vehicle pollutants can chemically degrade concrete, causing surface erosion, cracking, and strength loss. Protective coatings, chemical-resistant concrete mixes, and proper ventilation systems are effective preventive measures.
- Lack of maintenance. Neglecting routine maintenance exacerbates existing issues and leads to accelerated deterioration.
- Physical damage. Impact damage due to physical impact from vehicles or equipment causes localized damage to concrete.
- Water infiltration. Poorly sealed joints, cracks, and inadequate waterproofing systems allow water ingress into the structure, promoting corrosion, freeze-thaw damage, and chemical reactions within the concrete matrix.
Common Methods for Assessing Parking Garage Structural Integrity
Concrete investigation in parking structures is critical for assessing structural integrity, identifying deterioration issues, and planning effective repair and maintenance strategies. The following are some of the common methods used in the field:
- Visual inspection. Visual examination remains the initial and most fundamental inspection technique. It involves visually assessing concrete surfaces for signs of distress, including cracks, spalls, delamination, and surface defects. Visual inspection provides valuable insights into potential areas of deterioration and guides further investigation.
- Non-Destructive Testing (NDT). Various techniques are used to detect subsurface flaws without damaging the structure. Some of these techniques include:
- Ultrasonic testing (UT). UT utilizes high-frequency sound waves to assess concrete thickness, detect voids, and locate internal defects such as cracks and honeycombing. It provides detailed information about the condition of concrete elements without causing damage to the structure.
- Rebound hammer testing. Rebound hammer testing measures the surface hardness of concrete by striking it with a spring-loaded hammer and measuring the rebound velocity. This test provides an indication of concrete strength and helps identify areas of deterioration.
- Ground-penetrating radar (GPR). GPR uses electromagnetic waves to detect variations in subsurface materials, including concrete thickness, reinforcement location, and the presence of voids or anomalies. It is beneficial for locating embedded objects and assessing concrete conditions beneath the surface.
- Half-cell potential testing. Half-cell potential testing assesses the likelihood of reinforcement corrosion by measuring the electrical potential difference between embedded steel reinforcement and a reference electrode. It helps identify areas at risk of corrosion and prioritize maintenance efforts.
- Corrosion mapping. Corrosion mapping techniques, such as electrical resistivity mapping and corrosion potential mapping, are used to visualize and quantify corrosion activity within concrete structures. These techniques provide valuable data for prioritizing repair and maintenance activities and assessing the effectiveness of corrosion mitigation measures.
- Concrete core sampling. Concrete core sampling involves drilling and extracting cylindrical core samples from concrete elements for laboratory testing. Core samples are analyzed to evaluate concrete quality, compressive strength, chloride ion content, and other relevant properties. This information is used to assess the structural condition and performance of concrete elements.
- Structural analysis. Advanced computational tools are used to model the structure and predict its response to various stresses.
Parking Garage Repair and Maintenance Strategies
Repair and maintenance of concrete structures are crucial for prolonging their lifespan and ensuring safety. Strategies vary depending on the type of damage, environmental factors, and specific structural requirements. Common repair and maintenance strategies include:
- Concrete repair. Addressing areas of concrete deterioration through patching, crack sealing, and spall repair using appropriate repair materials such as epoxy mortars, polymer-modified concrete, and repair mortars.
- Corrosion mitigation. Implementing cathodic protection systems, corrosion inhibitors, and surface coatings to mitigate reinforcement corrosion and extend structural elements' service life in multi-level and underground parking garages.
- Waterproofing maintenance. Regularly inspect and maintain waterproofing membranes to ensure their integrity and effectiveness in preventing water infiltration into parking structures.
- Drainage system maintenance. Cleaning and maintaining floor drains, sump pumps, and drainage channels to prevent water accumulation and ensure proper drainage within multi-level and underground parking garages.
Parking Garage Collapse Incident and the Role of Structural Engineers
In April 2010, the parking garage of a building in Kingston, Ontario (the building) partially collapsed, resulting in extensive structural damage. The building consisted of a six-storey hotel and two underground parking garages. The incident occurred when the upper level of the two-storey underground parking structure collapsed, crushing the lower level and damaging cars (Figure 1). Although no injuries were reported, the collapse highlighted severe issues with the garage's structural integrity and maintenance. Investigations revealed multiple factors that led to the catastrophic failure, including:
- Concrete deterioration. Over time, environmental exposure to de-icing salts severely weakened the concrete structure. These salts penetrated concrete surfaces and accelerated the corrosion of steel reinforcements. Insufficient inspections and lack of timely maintenance allowed cracks to propagate, further accelerating the corrosion of steel reinforcement and undermining the structural integrity of the concrete slab (Figure 2 and Figure 3).
- Overloading during maintenance. The parking structure's resurfacing added additional load to the compromised structure, likely pushing the garage beyond its load-bearing capacity and causing the failure.
- Water and moisture penetration. Repeated freeze-thaw cycles caused by water infiltration into cracks exacerbated the deterioration. Moisture expanded within the concrete during freezing, leading to further cracking and material loss.
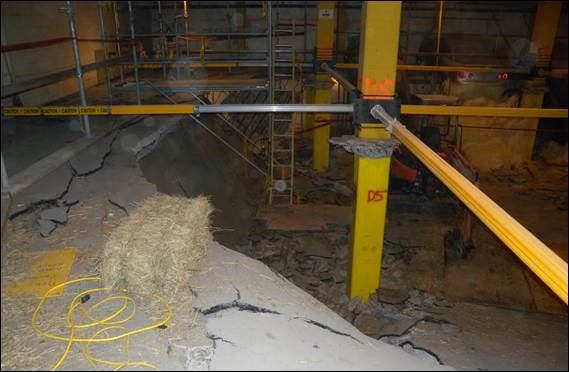
Figure 1 – Collapse of the upper level of the underground parking garage.
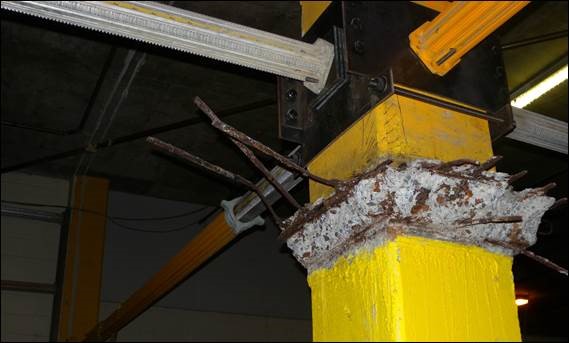
Figure 2 – Close-up of the column-slab connection shows the corrosion of reinforcement rebars.
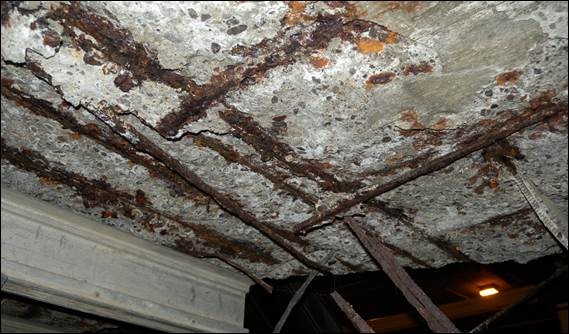
Figure 3 – A close-up of the underside of the concrete slab shows the severe corrosion of reinforcement rebars.
Roles of the Structural Engineer
It was reported that a structural engineer who was a guest at the hotel warned the hotel’s owner about the serious structural concerns in the parking garage before its collapse. The engineer highlighted the risk posed by the deteriorating concrete. Engineers have a professional duty to report imminent structural damage to authorities if they believe public safety is at risk. This duty is outlined in the engineering code of ethics and legal obligations, which prioritize public welfare and safety. If the property owner fails to take timely action or the risk is immediate, the engineer may have a legal obligation to report the issue to the appropriate authorities, including the Ministry of Labour.
After the underground parking collapsed, guests and staff were evacuated immediately. Structural engineers played a crucial role in responding to the parking garage collapse. Their responsibility included:
- Damage assessment. Structural engineers conducted inspections and detailed safety assessments to determine the extent of structural damage to the garage and its impact on the stability of the building’s upper levels. This was essential for ensuring the safety of emergency responders and guiding repair efforts.
- Stabilization planning. Structural engineers developed a plan to stabilize the building, including the use of shoring jacks to secure the structure (Figure 1 and Figure 2). This allowed safe access for workers and prevented further collapse during debris and vehicle removal.
- Vehicle securing. Structural engineers provided solutions, such as foaming suspended vehicles in place, to prevent additional load shifts or structural damage during removal.
- Designing repair. Structural engineers collaborated with contractors to create and implement a repair plan. This included removing damaged concrete and installing a new garage structure within the existing building.
- Regulatory coordination. Structural engineers worked closely with the Ministry of Labour and the City of Kingston, submitting daily engineered work plans and ensuring compliance with safety regulations.
Conclusion: How Structural Engineers Can Help
Structural engineers are indispensable in ensuring the safety and functionality of packaging garages. Through thorough assessment, including visual inspections, non-destructive testing, and corrosion detections, structural engineers identify potential risks and provide actionable recommendations for repair and maintenance. The role of structural engineers is not only critical in extending the lifespan of parking garages but also in ensuring the safety of the public and preventing catastrophic failures. Regular inspections and proactive maintenance strategies are essential for maintaining the integrity of parking garage structures.
Acknowledgments
We would like to thank our colleague Luaay Hussein, PhD, PMP, P.Eng. for providing insights and expertise that greatly assisted this research.